Solving EV Charging with High-Performance Gate Drivers and Current Sensors
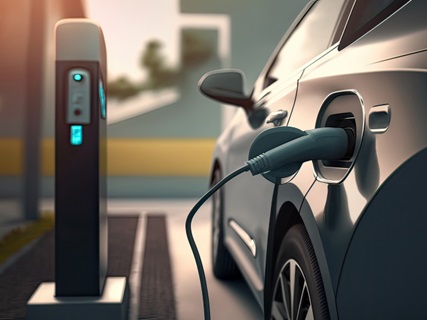
As government agencies and organizations commit themselves to the pursuit of a carbon-neutral future, electric vehicles (EVs) have been at the forefront of this revolution. Research indicates that electric vehicles are continually gaining a greater market share, with their contribution to total car sales having more than tripled from 4% in 2020 to 14% in 2022.
However, before EVs can reach true widespread adoption, one of the biggest obstacles is the accessibility, reliability, and performance of EV chargers.
From a technical perspective, achieving higher-performance EV charging necessitates a design focus on the under- lying power conversion systems, including AC/DC, DC/DC, and even DC/AC conversion (in the case of bidirectional charging). Improving these systems requires underlying electronic components that can operate more efficiently and accurately without sacrificing size, reliability, power throughput, and cost.
At Allegro, we are committed to enabling the future of EV charging by developing industry-leading gate drivers and current sensing solutions.
The Obstacles of EV Charging
Range anxiety is the consumer’s fear of an electric vehicle running out of power before reaching the destination or a suitable charging station. Today, experts consider this sentiment to be one of the largest obstacles to achieving widespread adoption of EVs. Within this, a major contributor to range anxiety is the inadequate charging infrastructure in the US and most of the world.
The first major shortcoming of existing EV charging infrastructure is the reliability of chargers. According to a J.D. Power report, 20.8% of EV drivers who use public charging stations have experienced being unable to charge their vehicles due to equipment failures. In many cases, these failures are the result of failures in the underlying elec- trical systems, including power electronics, connectors, and cabling.
Beyond reliability, the poor availability of chargers is a plague on the EV charging infrastructure. Research indicates that, in 2022, there were 55 EVs per charging location in the United States. Further complicating matters is the large geographic distances between charging stations, reducing consumer confidence that they can reliably take EVs on long trips.
Finally, charging speed is a major obstacle to EV charging. According to the US Department of Transportation, the average Level 2 charger can charge a light-duty EV in 4-10 hours. EV charging pales in comparison with the speed and convenience of gasoline refueling in internal combustion vehicles.
Meeting consumer expectations necessitates the ability to charge vehicles from 0 to 80% in less than an hour. Achieving such charging speeds will require higher-power DC charging solutions backed by robust, reliable, and efficient power electronics.
Ramifications for Future EV Chargers
Achieving this future will require integrating new materials and technologies into EV charging designs.
One such technology is wide-bandgap (WBG) semiconductors like silicon carbide (SiC) and gallium nitride (GaN). These materials offer superior characteristics for power transistors as compared to traditional silicon, including higher thermal conductivity, greater energy efficiency, and the ability to operate at higher voltages and temperatures.
Figure 2: Parameter Comparison of Si, SiC, and GaN
With more efficient operation, WBG materials enable more power-dense devices, meaning that future EV chargers will be able to provide more power in a smaller footprint. Furthermore, the efficiency improvements will allow for faster charging times by minimizing energy losses and associated thermal management, thereby enabling higher power charging without sacrificing reliability.
Additionally, the implementation of advanced circuit protection and intelligent feedback mechanisms will be essential for future EV chargers. Chargers will support features like self-diagnostics, real-time monitoring, and fault/anomaly detection by leveraging smart sensors and IoT technology. A combination of improved circuit protection technologies and more efficient WBG power devices will enable systems with greater levels of safety and reliability.
A Deeper Look at EV Charging Circuitry and the Crucial Role of Sensors and Drivers
The performance of EV charging systems hinges on the efficiency of their power conversion circuitry. Level 3 DC fast chargers perform AC/DC and DC/DC conversion within the charger itself, while Level 1 and 2 AC chargers rely on the vehicle’s onboard charger for this process. However, accurate current sensing is crucial for all charger levels.
Level 3 chargers utilize synchronous rectifier circuits with transistors to optimize power flow in their AC/DC and DC/ DC conversion stages. These systems depend heavily on real-time feedback from current sensors to dynamically adjust gate driving signals, maximizing efficiency and minimizing power loss.
While Level 1 and 2 chargers don’t perform the power conversion, they still require precise current measurement for safety and control. Monitoring the current flow allows these chargers to:
- Ensure Safe Charging: By constantly measuring the current delivered to the vehicle, Level 1 and 2 chargers can detect overcurrent conditions and automatically shut down to prevent damage to the vehicle’s battery or the charger itself.
- Communicate with the Vehicle: The charger uses current sensing to communicate with the EV’s onboard charger, ensuring the charging current is within safe limits and optimizing the charging process based on the battery’s state of charge.
Current sensors provide the system with data on the magnitude and direction of current flowing through the circuits, enabling the system to:
- Optimize Switching: By monitoring current flow, the microcontroller can dynamically adjust the gate driving signals to maximize efficiency and minimize power loss (in Level 3 chargers).
- Enhance Safety: Current sensors detect overcurrent and fault conditions, protecting components and preventing hazards like short circuits.
Allegro’s current sensors and gate drivers play a critical role in both Level 3 and Level 1 and 2 charging systems. We offer both TMR (tunneling magnetoresistance) and Hall-effect current sensors, each with unique strengths.
- TMR Sensors: ideal for high-precision applications requiring high bandwidth, accuracy, and fast response Due to their speed and isolation capabilities, they are particularly well-suited for WBG semiconductor applications.
- Hall-Effect Sensors: Offer a cost-effective solution for applications where extreme precision is less critical. Allegro’s innovative packaging with integrated ferromagnetic concentrators reduces size and cost.
Gate drivers act as the crucial link between the control signals and the power devices (like WBG FETs), ensuring precise and efficient switching. Allegro’s gate drivers, featuring Power-Thru technology, simplify system design and maximize the benefits of WBG switches. Key advantages include:
- Integration: Combining an isolated gate driver and power supply in a single package eliminates the need for external components, reducing size and complexity.
- Efficiency: Reduced common-mode capacitance and fast slew rates minimize power loss during switching, leading to higher overall efficiency.
- Design Simplicity: Simplified dead-time management and optimized drive characteristics streamline the design process for GaN-based systems.
Towards a Carbon-Neutral Future
EVs are a crucial piece of the equation for achieving a carbon-neutral future. But, before we can achieve widespread adoption of EVs, the industry must first overcome the major challenges in EV charging.
With industry-leading current sensing and gate-driving solutions, Allegro is committed to enabling the EV revolution and creating a more sustainable future. To learn about Allegro’s product offerings, read more at https://www.allegromicro.com or contact our sales department at https://www.allegromicro.com/en/about-allegro/contact-us/sales-offices-and-distributors.
The electric vehicle revolution is here, but are we ready to power it? Consumers are eager to embrace electric vehicles, but concerns about charging time, cost, and infrastructure remain major roadblocks to widespread adoption. Learn how Allegro is shaping the future of EV charging and partnering with manufacturers to accelerate the transition to a sustainable electric future in our recent whitepaper.
Copyright 2025, Allegro MicroSystems.
The information contained in this document does not constitute any representation, warranty, assurance, guaranty, or inducement by Allegro to the customer with respect to the subject matter of this document. The information being provided does not guarantee that a process based on this information will be reliable, or that Allegro has explored all of the possible failure modes. It is the customer’s responsibility to do sufficient qualification testing of the final product to ensure that it is reliable and meets all design requirements.
Copies of this document are considered uncontrolled documents.