Overcoming Complexity Challenges in PCB Design with Magnetic Current Sensors
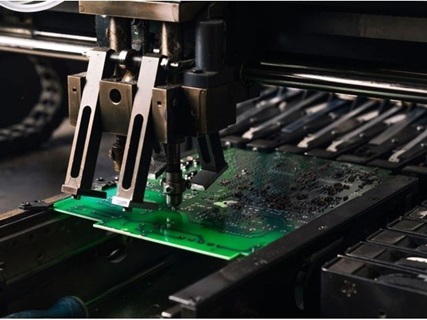
Article 3 of Next-Generation Current Measurement Series: Magnetic current sensors streamline PCB design by accurately measuring current through magnetic fields to reduce complexity in modern electronics.
Introduction
Magnetic current sensors are revolutionizing PCB design by offering simpler solutions to traditional current measurement methods. These sensors integrate multiple components into a single IC to reduce design complexity and enhance overall system performance.
This article explores how magnetic current sensors address complexity issues in PCB design, focuses on their advantages over conventional methods and provides insights through a detailed case study.
In our Next-Generation Current Measurement series, we've previously explored various challenges associated with traditional current sensing methods. This article focuses specifically on addressing the challenge of complexity within PCB design and highlights the advantages of magnetic current sensors in modern electronics.
Complexity Challenges in Traditional Current Sensing Methods
Traditional current sensing methods, as previously highlighted in this series, present a range of challenges that significantly complicate the design and functionality of PCBs. These methods typically rely on shunt resistors (along with additional components), which are prone to generating substantial heat, necessitating more complex thermal management systems than non-shunt solutions. As a result, traditional methods end up consuming valuable PCB space with additional components like heat sinks.
Beyond the issues of space and heat, shunt resistors introduce electrical and design complexities. They inherently possess inductance, which leads to voltage spikes when there is a rapid change in current. This behavior can disrupt other sensitive components and skew the measurement accuracy, which presents a significant challenge in maintaining the integrity and reliability of the system. Additionally, the impedance of a shunt resistor increases with frequency due to this inductance, thereby resulting in notable sensitivity changes at higher frequencies.
For example, a high-end shunt resistor with a 200 µΩ resistance and 3nH inductance, which can cost more than $0.15 and occupy over 50 mm² space on the PCB, suffers from performance degradation at bandwidths exceeding 10 kHz. The inductance impacts the shunt's operation by affecting its performance at high frequencies and necessitates the integration of additional components to mitigate the resultant issues.
Mitigation Strategies in Conventional Systems
To address these voltage spikes and other inductive effects, traditional systems often require external components to filter the shunt voltage. This process adds to the design complexity as it involves the careful tuning of filter components based on the system's specific requirements to ensure the amplifier's input stage is protected from saturation during high transient switching events.
The design of these filters makes it necessary to use precision components to maintain its performance parameters like a high common-mode rejection ratio and pole location, which involve the use of low-value resistors to minimize effects due to input bias currents and also high-precision capacitors and resistors. These components can be large and costly, which further complicates the PCB design and adds to the overall system cost. Achieving an accuracy of less than 1% over various frequencies typically requires specialized tuning, including trial and error, which is both time-consuming and expensive.
Impact of Complexity on Solution Cost
The complexities involved in traditional current sensing methods escalate the overall solution cost. The necessity for precision components, extensive protective measures against electrical noise and spikes, and the labor-intensive design process not only increases the direct materials and manufacturing costs but also extends development cycles. This increased expenditure can affect the profitability and market competitiveness of products, particularly in industries where rapid innovation and cost efficiency are critical.
Minimizing PCB Design Complexity with Magnetic Current Sensing
Magnetic current sensors represent a significant advancement in current sensing and offer a comprehensive solution that integrates multiple functions into a single component. This integration streamlines the design process and minimizes the space requirements.
Streamlined Design Process
Magnetic current sensors incorporate integrated signal conditioning, which eliminates the need for additional filtering and complex components. This simplifies the PCB layout by reducing the number of components and enhances the overall system reliability by minimizing potential failure points. The factory calibration of these sensors ensures consistent performance across diverse temperatures and operational conditions to alleviate the need for extensive calibration by the end-user.
Enhanced Measurement Accuracy
Unlike traditional shunt systems that require high levels of amplification for low-resistance measurements—often introducing noise and potential errors—magnetic current sensors maintain accuracy and reliability without the need for such amplifications. These sensors come factory-calibrated to ensure consistent performance across a broad temperature range and to enhance their reliability. This inherent stability makes them effective in environments where interference or noise could compromise the system’s functionality and provide a dependable solution even under variable operating conditions.
Economic Advantages
Magnetic current sensors reduce the number of components required on the PCB, thereby lowering material costs and simplifying assembly. This decrease in component count can lead to fewer manufacturing errors and less rework to ultimately reduce overall production costs. Additionally, the diminished need for specialized components and extensive laboratory testing can further lower development expenses to make the design-to-production process more economically efficient.
Flexibility in Applications
The versatility of magnetic current sensors allows for their use in various configurations, such as low-side, high-side, and in-line applications. Moreover, these sensors can handle extensive voltage ranges making them suitable for a broad spectrum of industrial applications.
This integration streamlines design and manufacturing processes, and opens new avenues for innovation in PCB design, enabling engineers to focus more on enhancing functionality rather than navigating technical hurdles.
Accelerated Development and Deployment
The simplified design enabled by magnetic current sensors can significantly expedite the product development process. With fewer components to integrate and test, the timeline from concept to market-ready product can be shortened. In rapidly evolving industries, this faster time-to-market is invaluable and provides a substantial competitive edge by enabling quicker responses to market demands and technological advancements.
Case Study: Clean Energy Solar & Storage System Manufacturer
A prominent example of the benefits of magnetic current sensors can be seen in a case study involving a clean energy solar and storage system manufacturer in the United States. This company faced considerable challenges with the complexity of traditional shunt resistors for current sensing across multiple points in their systems. Each additional sensing point introduced complexity due to the need for accurate filter design and variability management of passive components over temperature and lifespan.
Challenge Faced
The manufacturer required a current sensing solution that could be implemented efficiently within the tight size and performance constraints of their innovative solar and storage systems. Traditional methods were proving too cumbersome, time-consuming and prone to error, which impeded rapid development and scaling.
Solution Delivered
After looking at various options, the brand decided to switch to Allegro’s ACS711 magnetic current sensor. This sensor offered a drastically simplified installation process due to its integrated signal conditioning and factory calibration, which eliminated the need for additional filtering and on-site calibration.
Outcome Achieved
The adoption of the ACS711 allowed the manufacturer to streamline their design considerably. This simplification reduced the overall design time and manufacturing costs, facilitated a faster transition from prototype to production and ultimately accelerated the time-to-market for their products. The flexibility of the ACS711 to be used in various applications also allowed the company to standardize their sensing approach across different parts of their system, thereby simplifying inventory and maintenance.
Overcoming Complexity Challenges in PCB Design with Magnetic Current Sensors by Allegro MicroSystems
The ACS37041 and ACS37220 from Allegro MicroSystems exemplify the advancements in magnetic current sensing technology that significantly reduce design complexity while enhancing performance in modern electronics.
Allegro ACS37041: This sensor is housed in a compact SOT23-W package, ideal for space-constrained applications. It supports current measurement up to 30A and operates up to 100V(RMS), which makes it versatile for applications in power, manufacturing, automotive, and other sectors. Its low resistance of 1 mΩ and an error below ±5% across temperature variations ensure precise current measurement without the need for external calibration, thereby simplifying the design process.
Allegro ACS37220: Designed for high-current applications, the ACS37220 can handle up to 200A and also operates under 100V(RMS). It features ultra-low resistance of 100 μΩ and is AEC-Q100 certified, which is crucial for reliability in automotive environments. The sensor is encased in a 4 x 4 mm QFN package and optimal for applications that demand high performance in a minimal footprint.
Both sensors embody the integration of advanced signal conditioning features, which eliminate the need for additional filtering and ancillary components. This integration saves PCB space and reduces the potential for errors during the design phase, thus streamlining the development process and accelerating the time-to-market for new products.
Conclusion
Magnetic current sensors have demonstrably overcome many of the complexities associated with traditional PCB design for current sensing. By reducing design complexity, enhancing reliability and cutting costs, these sensors support a more innovative approach to electronics design.
This article concludes our Next-Generation Current Sensing series. Throughout this series, we explored how magnetic current sensors, particularly those developed by Allegro MicroSystems, revolutionize PCB design by addressing size, heat, and complexity challenges. The cutting-edge solutions by Allegro MicroSystems set new industry standards for current measurement.