Rethink What Is Possible for PCB Current Sensing
Introduction
Across all markets, from renewable energy and motor drives to electric vehicles, electronic devices are challenged to be smaller, more efficient, and less expensive. This increases the complexity of printed circuit board (PCB) designs and pushes engineers to find innovative solutions. Because all these solutions require power, electrical current (I) and voltage (V) must be sensed and are mission critical in these applications. Having accurate current sensing makes controlling, protection, and monitoring feasible at various levels in the system.
When it comes to selecting the right current sensor for PCB designs, current handling capabilities becomes increasingly important. Current measurements in PCBs often max out at about 100 A due to thermal limitations within the PCB. Going higher than 100 A generally requires a complex solution that can translate into a bigger size and higher associated costs. However, being able to measure PCB currents reliably above 100 A can also offer great advantages such as efficiency improvements and overall system-level cost reductions.
Two common current sensing methods used today are shunt resistors and magnetic sensors. Both solutions use the voltage developed across a small-valued resistor (shunt) or a magnetic sensing element (such as Hall effect) with an integrated conductor to interpret the current value. While shunt methods usually offer very good resolution and accuracy, they suffer from energy inefficiency due to their ohmic losses and increased layout complexity associated with the shunt resistor connection and changing solder resistance over lifetime. Newer magnetic sensor options overcome these limitations – by offering standalone integrated solutions that make PCB current measurements up to 600 A possible due to their very small ohmic losses and compact size.
This article will discuss two new innovative approaches to measure currents up to 600 A in PCB: a near lossless Hall-based current sensor with an integrated conductor and a non-invasive standalone core-free and shield-free differential Hall current sensor.
Near lossless Hall-based current sensors with an integrated conductor
Electronic devices in various markets are seeing increasing needs for higher current density solutions to increase their overall efficiency and lower their cost. For example, power conversion applications such as DC/DC converters and on-board chargers are seeing a rapid increase in their current density due to the increased adoption of wide bandgap transistors like silicon carbide (SiC) to enable circuit miniaturization and improve the overall efficiency of the system. Current sensors in these applications ideally need to be compact, efficient, accurate, and offer high bandwidth to capture the very fast current wave that these high switching transistors produce.
There are two popular solutions to this challenge today – shunt resistor-based solutions and magnetic sensors. For magnetic sensor options, Allegro MicroSystems offers a broad range of very low resistance, highly integrated current sensor packages with different current and voltage handling capabilities. Existing shunt solutions require complex layout and circuit implementation to achieve high current and voltage levels and typically have higher resistance. In contrast, Allegro’s current sensors are differentiated by their compact size and ease of use, as highlighted in Figure 1.
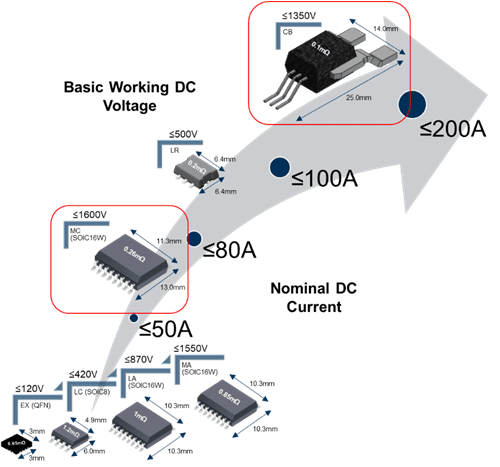
Recently, Allegro has introduced two new surface-mount package options that can measure currents up to 500 A. The first is a module-like custom package that can detect currents up to 500 A with very small resistance (100 µΩ), while providing excellent working isolation voltage rating — a 1350 V basic working voltage. Dubbed the “CB” package, this has an integrated internal ferromagnetic concentrator that directs field from the current-carrying trace into the sensitive plane of the Hall element. Figure 2 indicates the different components that come together to form the CB package. Current travelling through the leadframe creates a magnetic field directed by the concentrator into the IC. The signal pins exit the overmolded package for connections to external circuitry. The nature of Hall-effect-based current sensors allows for inherent isolation, as the current-carrying leadframe does not need to be electrically connected to the IC. Plastic mold compound within the CB package also insulates the IC and signals pins from the leadframe. The CB package has been certified to UL specification 60950.
This package is a unique solution for high-density PCB design that allows customers to shrink their overall size with a simple, easy-to-use current sensor compared to other expensive, bulkier, and more complicated solutions such as shunts or larger modules. More details about the thermal performance can be found in this app note. Other alternative high current density packages include Allegro’s tiny (6.4 × 6.4 mm2) custom LR package, which can handle up to 500 V DC working voltage and 100 A+ current. A third offering is the new custom SOIC16W (MC) package that has a thick leadframe that allow this package to pass 80 A+ while offering excellent 1600 V basic isolation voltage. Figure 3 highlights the different packages temperature rise as various continuous current levels.
Standalone, non-invasive, core-free and shield-free Current Sensors
For applications that require non-invasive, high current density solutions, Allegro has recently introduced a new family of coreless current sensors, including the new ACS37612. This product family offers a true standalone solution for current measurement; these solutions enable designers to remove the cores and shields from their designs. These sensors measure currents up to 600 A flowing through a PCB with a typical accuracy of 1%. The differential Hall elements used to measure the magnetic field provide great immunity to stray magnetic fields without the need of a laminated shield required by competing solutions, which reduces the design size and bill of materials (BOM). See figure 4 for a basic overview of the principle of operation and implementation.
A: Basic theory of operation
B: Implementation method in a PCB
A typical application for such a solution is a traction inverter in electrical vehicles. During acceleration, hundreds of amps flow through the traction motor inverter. A precise measurement of such high currents is vital for safe operating performance. Engineers have traditionally relied on a low-hysteresis laminated core for such measurements—using three to six cores, depending on the number of phases in the motor.
The system coupling factor, which determines the current dynamic range, is determined by the sensitivity level of the ACS37612 and the PCB’s metal trace. The needed modification to the current carrying traces adds very small resistance, ~50 µΩ. This provides designers with a lot of manufacturing flexibility and the ability to easily increase the current sensing range at any phase of the design.
Eliminating the cores with the ACS37612 allows manufactures to reduce the space and weight of the inverters, thus increasing the efficiency of the electric vehicle. This non-invasive, contactless current sensor is designed to improve thermal efficiency relative to shunt solutions and is therefore ideal for reducing system energy consumption in 48 V e-motor platforms and high voltage inverters.
Conclusion
With the advancement of electronic systems, the need for efficient, high current capable, efficient PCB current sensors is becoming more important than ever due to the critical role that current measurements play. With simple, easy to use surface-mount current sensors, Allegro’s line of integrated conductor solutions addresses the market needs in terms of current and voltage isolation capabilities. For even more flexibility, designers may gravitate toward Allegro’s new coreless current sensors for true standalone, lossless, non-invasive current measurement. Both of these solutions set new standards on what is possible for PCB current sensing, allowing system designers to achieve new levels of efficiency and power density.
Originally published in Elektronik Industrie, April, 2020. The original article can be found online here. Republished with permission.
- Download Original PDF [German]