Current Sensors in Robotics: Precision, Efficiency, and Safety in Every Movement
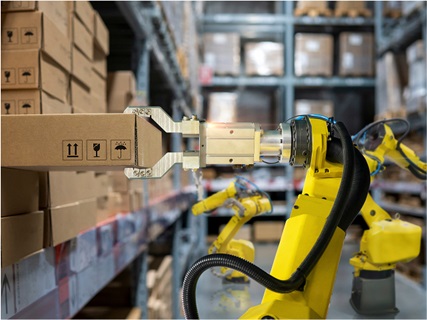
The world of robotics is rapidly evolving. We marvel at robotic arms assembling intricate electronics with superhuman precision, surgical robots performing minimally invasive procedures with unparalleled dexterity, and autonomous vehicles navigating complex environments with seemingly effortless grace. But behind these impressive feats of engineering lies a critical, often unsung hero: the current sensor. These small but mighty components are the linchpin of modern robotics, providing the essential feedback mechanism that allows robots to interact with the world accurately, efficiently, and safely.
Current sensors are the bridge between a robot's "brain" (the control system) and its "brawn" (the motors), constantly monitoring the electrical current flowing through the motors. This current flow is directly proportional to the torque, or rotational force, that the motors generate, providing a real-time window into the robot's physical exertion. Monitoring this continuous feedback loop is the foundation upon which precise motion control is built. Without accurate and responsive current sensing, robots would be clumsy and unpredictable, unable to perform the delicate maneuvers required in fields like manufacturing, surgery, and autonomous navigation. Imagine a robot arm attempting to place a tiny component on a circuit board without knowing the exact force it's applying – the result would likely be a broken component or a damaged board. Current sensors not only enable precision but also play a vital role in optimizing energy efficiency. By closely tracking current draw, the control system can fine-tune the power delivered to each motor, minimizing wasted energy and maximizing battery life. This is especially critical for mobile robots, such as those used in warehouses, exploration, or delivery services, where extended operating time is paramount.
Furthermore, current sensors are essential for ensuring the safety of robots and the people who work with them. They can rapidly detect overcurrent conditions, which can occur due to motor overloads, short circuits, or other faults. The sensor can trigger protective shutdowns, preventing damage to the robot, its surroundings, and potentially preventing injury to nearby humans.
A Potential Solution: A Small Chip with a Big Impact
Let's delve deeper into a specific example: the Allegro MicroSystems ACS37030/32 high bandwidth current sensor. These devices are purpose-built for the demanding world of robotics. Drones, compact collaborative robots (cobots), and miniature medical robots all require high performance packed into tiny spaces. The ACS37030/32 delivers precisely that in a small 4.9x6mm package. These devices employ a clever dual-path sensing architecture. A Hall-effect sensor captures DC and low-frequency current information, while an inductive coil handles the high-frequency components. This ingenious combination results in a wide bandwidth, spanning from DC all the way up to 5 MHz, capturing the full spectrum of current dynamics. The 40 ns typical response time enables real-time control even in the most dynamic robotic applications. The devices can be configured for three sensing ranges +/- 20A, +/-40A or +/-65A. Accuracy is paramount, and these chips deliver with a ±2% sensitivity error over temperature and a low input-referred noise of 50 mARMS, ensuring consistent performance and clean signals.
Beyond the Specs: Features that Matter in Robotics
But the ACS37030/32's value extends beyond raw performance figures. It's the thoughtful features that truly make these chips stand out in the robotics world. For instance, the ACS37030 offers a dedicated reference voltage output (VREF) for differential routing. This is a crucial advantage in the electrically noisy environments often found in robotic systems, especially compact ones, where close proximity of components can lead to interference. Differential routing, using the VREF, helps to reject common-mode noise and ensures clean, accurate current measurements. The ACS37032 variant takes safety a step further by incorporating a dedicated fault output for overcurrent detection. This feature is invaluable for preventing damage from overloads or short circuits, which are particularly concerning in smaller robots where space constraints can increase the risk of such events. Both the ACS37030 and ACS37032 are housed in a compact 6-pin SOIC package, minimizing their footprint and simplifying integration into space-constrained designs. Moreover, the AEC-Q100 Grade 0 qualification signifies these chips meet stringent automotive-grade reliability standards, guaranteeing robust performance even in the harshest robotic environments. This high level of reliability is essential for applications where failure is not an option, such as in autonomous navigation or critical safety systems.
Powering the Future of Robotics, Big and Small
The low power consumption (20mA typical at 3.3V) and low internal conductor resistance (0.68 mΩ typical) of the ACS37030/32 are particularly advantageous in smaller robots, where battery life is often a major design constraint. These features contribute to maximizing operational time and minimizing power loss due to heat dissipation. This efficiency is especially important for mobile robots and drones, where every milliwatt saved translates to extended range and mission capabilities. Beyond the essentials of motion control, efficiency, and safety, current sensors like the ACS37030/32 are enabling advanced robotics functionalities. They are the key to force sensing and control, allowing robots to interact with their environment with a delicate touch. They also enable predictive maintenance by detecting subtle changes in motor performance, paving the way for proactive repairs and minimizing downtime. In the collaborative robotics space, current sensors are essential for ensuring the safety of human-robot interactions, triggering immediate stops in the event of accidental contact. Whether it's a large industrial robot or a small, agile cobot, current sensors are empowering the next generation of robotics. They are the bedrock of precision, efficiency, and safety, shaping a future where robots work seamlessly and safely alongside humans.
The future of robotics is inextricably linked to advancements in sensing technology. Current sensors, like the innovative ACS37030/32 from Allegro MicroSystems, are not merely components; they are the foundation upon which intelligent, efficient, and safe robots are built. As robots continue to integrate into various aspects of our lives, the crucial role of current sensing will only become more pronounced, empowering a new era of human-robot collaboration and innovation. These sensors are the silent force behind every precise movement, every efficient operation, and every safe interaction, shaping a future where robots and humans work together seamlessly to achieve the extraordinary.
To learn more about Allegro’s solutions in robotics, visit here.