Next-Generation Current Measurement: Addressing PCB Design Challenges with Magnetic Current Sensors
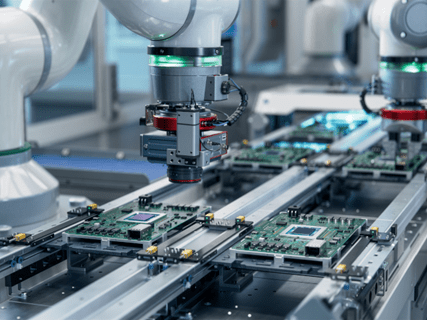
Introducing the Next-Generation Current Measurement Series: Advanced magnetic current sensors accurately detect magnetic fields generated by current flow, offering precise current level measurements.
Introduction
Precision current measurement is essential for optimizing performance and protecting components in various systems. Traditional methods use shunt resistors and operational amplifiers to convert current to a measurable voltage signal. However, these methods have significant challenges, such as heat generation, large PCB footprints and design complexity.
This article explains the necessity of efficient current sensing and compares traditional shunt with advanced magnetic sensors. Highlighting their advantages in terms of size, heat management and design simplicity, it also introduces key current measurement products by Allegro to showcase these benefits and provide engineers with insights into their applications and impact on modern electrical systems.
This article is a part of Next-Generation Current Sensing, a series that delves into innovative developments in current measurement technology.
The Need for Space and Power Efficiency in Current Sensing
Accurate and efficient current sensing is critical in modern electrical systems for several reasons. It is essential for monitoring, controlling and protecting electrical components and systems.
Here’s how current sensing plays a crucial role in various applications:
Motor Drives: Current sensors in motor drives are critical for regulating and controlling the performance of electric motors used in various industrial and commercial applications. These sensors enable precise control of motor speed and torque by providing real-time feedback on the current being consumed. This capability is essential for optimizing the motor's efficiency, ensuring energy conservation and protecting the motor from potential damage due to overcurrent conditions. By maintaining exact current levels, these sensors also contribute to the longevity and reliability of motor systems to make them indispensable in modern automation and machinery.
Precise current sensing on an electric motor drive ensures optimal performance and efficiency to protect the device and enable smooth operation.
Battery Management Systems (BMS): In Battery Management Systems, current sensors play a pivotal role by continuously monitoring the current that flows into and out of the battery. This data is crucial for calculating the battery's state-of-charge (SoC) and state-of-health (SoH), which are key to optimizing battery performance and lifespan. Accurate current measurement ensures that batteries operate within their safe operating area to prevent conditions such as overcharging or deep discharge, which can significantly affect battery health and safety.
Power Converters: Current sensors are essential components in power converters, where they facilitate the efficient transformation of electrical energy from one form to another (e.g., AC to DC, DC to AC, or changing voltage levels). These sensors enable precise control of the power conversion process to minimize energy losses through optimal switching times and enhance the quality of the output power.
Current measurement in these power electronic solutions not only improves the overall system efficiency but also enhances the reliability and safety of devices that rely on these converters, such as renewable energy systems, consumer electronics and industrial machinery. Some industries where the use of current measurement is particularly critical include:
Clean Energy: In these systems like solar panels and wind turbines, accurate current sensors help manage instantaneous power output, which is crucial for matching production with demand and maintaining grid stability.
Electric Vehicles (EV): In electric vehicles, current sensors play a crucial role in multiple systems. They are used in battery management to precisely monitor charge states and adjust charging cycles, thereby extending battery health and enhancing safety. Current sensors help regulate motor drives for vehicle propulsion. They also control the motors in the electronic power steering system to ensure precise handling. Additionally, they monitor systems like infotainment and power outlets to ensure these features operate within safe electrical parameters and are protected from electrical overloads.
Furthermore, extending beyond the vehicle itself, current sensors in EV chargers are essential for monitoring the charging current to ensure efficient and safe charging operations.
Data Centers: Current sensors are also utilized in data center server power supply and backup systems, playing a crucial role in maintaining stable and efficient operation. They help monitor and manage the electrical load to ensure optimal performance and reliability of these critical components.
Industrial Applications: To enhance performance and safety, current sensors are indispensable in a range of industrial applications. For e-bikes, they monitor battery load to optimize power management and extend battery life. In autonomous guided vehicles (AGVs) used in logistics and manufacturing, these sensors are crucial for regulating power consumption to ensure efficient and safe operation. Additionally, current sensors help manage energy usage in power tools to prevent overheating, prolong the lifespan of the tools and safeguard the equipment and the user.
Consumer Electronics: Current sensors are crucial for detecting and preventing abnormal current draw in consumer electronics. For instance, they monitor smartphone charging to prevent overcurrent, manage power distribution in laptops and regulate power supplies in TVs to protect against spikes that could damage sensitive circuits.
The Fundamentals of Current Measurement
Direct measurement of current in electrical systems is not practical due to the inherent difficulties in capturing and interpreting the flow of electrons. Instead, the current is converted into a measurable voltage signal using current sensors, a process crucial for effectively utilizing current data across various applications. This conversion involves two main steps:
Current-to-Voltage Conversion: The first step in measuring current involves converting the current flow into a corresponding voltage signal, which is typically achieved through shunt resistors or magnetic current sensors. The resulting voltage signal is then ready for further processing.
Signal Conditioning: Once converted into a voltage signal, the current often requires amplification and conditioning to be usable by the system. This step involves filtering out noise, amplifying the signal to a detectable level and stabilizing it to ensure accuracy across different operating conditions. Signal conditioning is essential for ensuring that the current data measured is both precise and reliable.
Shunt Resistors: The Traditional Approach
Shunt resistors, also known as current shunts or current sense resistors, have been the foundation of current sensing for many years. They operate based on an implication of Ohm's Law (V∝I), which states that the voltage drop across a resistor is proportional to the current flowing through it. Let us take a closer look at their operation and the challenges they present.
Operation of Shunt Resistors
When current flows through a shunt resistor, a small voltage drop is created across the resistor. This voltage drop is directly proportional to the current flow and makes it possible to measure the current by measuring this voltage. However, the voltage generated by the shunt resistor is typically very small and needs to be amplified to be useful. This is where current sense amplifiers, or shunt amplifiers, come into play. These amplifiers apply a gain (Av) to the input signal and produce an output voltage (VOUT = AvV) that the system can detect and act upon.
Current measurement using a shunt resistor.
The value of the shunt resistor must be kept as low as possible to minimize power dissipation and heat generation. However, it must be just high enough to produce a detectable voltage drop that can be accurately measured. This delicate balance ensures that the resistor does not introduce significant resistance into the circuit while providing a sufficient signal for accurate current measurement. Selecting the appropriate shunt resistor value is crucial for maintaining system performance and accuracy.
Drawbacks of Shunt Resistors
Despite their widespread use, shunt resistors come with significant drawbacks:
- Large Footprint: Shunt resistors, along with their associated components such as amplifiers and filters, consume substantial PCB space. This can be a limiting factor in compact designs where space is premium.
- Heat Generation: Power dissipation in shunt resistors is a significant issue. The power dissipated as heat (P = I²R) can affect the system's performance and may require additional cooling solutions, which further increases the design's complexity and cost.
- Design Complexity: Designing an effective current sensing system using shunt resistors requires expertise in filter design and careful consideration of variations in passive components over temperature and time. This adds to the design complexity and can be a time-consuming process.
- Accuracy Limitations: The accuracy of shunt resistors can be affected by temperature changes and the resistors' precision. Ensuring high accuracy often requires high-quality, precision resistors, which can be costly.
Given these challenges, alternative current sensing solutions that offer improved performance, efficiency and simplicity are clearly needed.
Magnetic Current Sensors
Magnetic current sensors operate based on the principle of detecting the magnetic field generated by current flow through a conductor. Here is a detailed explanation of how these sensors work:
Operation of Magnetic Current Sensors
When an electric current flows through a conductor, it generates a magnetic field around the conductor. This phenomenon is governed by Ampère's Law, which states that the strength of the magnetic field (B) around a conductor is directly proportional to the electric current (I) flowing through it and inversely proportional to the distance (D) from the conductor:
Where 𝜇0 represents the magnetic permeability of free space.
This fundamental principle forms the basis for how magnetic current sensors, such as Hall-effect sensors, work. Key steps in the operation of these sensors include the following:
Magnetic Field Generation: As the primary current (IIN) passes through the conductor, it creates a circular magnetic field around the conductor. This field's intensity (BIN) varies with the current magnitude and the distance (D) from the conductor.
Hall Element Placement: A Hall element—a small, flat semiconductor device—is strategically placed perpendicular to the direction of the magnetic field.
Current measurement using an integrated magnetic current sensor.
Voltage Induction (Hall-effect): When the magnetic field penetrates the Hall element, it exerts a force on the charge carriers (electrons) moving within the Hall sensor due to the primary current. This force displaces the electrons towards one side of the Hall element to create a voltage across the element, known as the Hall voltage. This voltage is perpendicular to both the current direction and the magnetic field.
Voltage Output: The Hall voltage is proportional to the magnetic field strength, and thus, to the primary current. The sensor circuit typically amplifies this voltage to a usable level, which results in an output voltage (VOUT) that serves as a measurable representation of the current flowing through the primary conductor.
Current Sensing: The output voltage (VOUT) from the Hall sensor can be directly correlated to the current magnitude in the primary conductor, which allows the sensor to provide a real-time measurement of current without any physical contact with the primary conductor.
Magnetic current sensors from brands like Allegro integrate advanced signal conditioning within their current sensing IC to include:
- Amplification: Boosting the small voltage signal to a level the system can easily interpret.
- Filtering: Removing noise and unwanted signals to ensure a clean output.
- Compensation: Adjusting the signal to account for temperature variations ensures consistent accuracy across various operating conditions.
Advantages of Magnetic Current Sensors
By addressing the limitations of shunt resistors, magnetic current sensors provide a more efficient, compact and reliable solution for current measurement. Some benefits of using magnetic current sensors include:
- Isolated Non-intrusive Measurement: Magnetic current sensors offer a non-contact method of current measurement to avoid direct interaction with the current-carrying conductor. This functional isolation not only mitigates the risk of voltage spikes damaging system components, as often seen with shunt resistors during switch operations, but it also ensures wide tolerance for over- and under-voltage conditions. Unlike shunt solutions, which may require tuning of system parameters like rise/fall times to manage voltage spikes, magnetic sensors maintain measurement accuracy and system integrity without the need for additional protective components or adjustments. An in the Next-Generation Current Measurement series will further examine this.
- Lower Heat Generation: Magnetic current sensors dissipate significantly less heat due to their lower inherent resistance than shunt resistors. This reduces the need for additional cooling mechanisms. More insights on this topic to come in a from the Next-Generation Current Measurement series.
- Simplified Design: With integrated signal conditioning and factory calibration, magnetic current sensors eliminate the need for external filters and extensive design adjustments. This simplifies the design process, which reduces development time and cost. Magnetic current sensors typically occupy less PCB space as they integrate multiple functions into a single IC. This compact design allows more efficient use of board space and enables more streamlined system designs. The series will explore this further in an .
- High Accuracy and Reliability: Magnetic current sensors provide accurate measurements across a wide range of operating conditions. Factory calibration ensures consistency and reliability to make them suitable for high-precision applications.
- In-line Current Sensing: Magnetic current sensors like the ACS series simplify in-line current measurements by providing direct readings, which avoids the complexities of low-side switch methods that require MCU synchronization with PWM and fail to measure when the switch is off. Unlike shunt methods plagued by high-frequency transients and ground bounce, ACS sensors directly measure in series with the load and are immune to conductor impedance changes. This setup eliminates the need for additional components to make ACS sensors ideal for accurate and efficient in-line current sensing in technical applications.
Magnetic current sensors from the Allegro’s ACS series simplify in-line current measurements by providing direct readings and avoids the complexities of low-side switch methods that need MCU synchronization.
- Better Common Mode Transient Immunity (CMTI): Magnetic current sensors, such as the Allegro’s ACS series, offer superior performance advantages in motor control applications by minimizing interference from common mode transients. They reduce blanking time, thereby maximizing the duty cycle. Unlike operational amplifiers that can exhibit ringing due to lower CMRR and shunt inductance (V = di/dt x L), ACS sensors are specifically designed to reduce ringing caused by rapid voltage changes (dV/dt) and are immune to the voltage spikes associated with inductance. This results in improved current step response by providing more accurate feedback and finer control over motor operations.
Magnetic current sensors from the Allegro’s ACS series enhance motor control by minimizing interference from common mode transients.
- High Bandwidth: Silicon Carbide (SiC) and Gallium Nitride (GaN) components, prone to rapid thermal runaway, demand swift overcurrent protection that Allegro’s magnetic sensors deliver with their ability to respond within 100ns. Unlike traditional shunt solutions that lose effectiveness at high frequencies due to impedance-induced sensitivity fluctuations, ACS magnetic current sensors maintain a stable response up to 5 MHz without needing additional tuning to make them optimal for high-performance applications.
Allegro's Magnetic Current Sensors
Allegro MicroSystems is a leading brand in the field of sensor integrated circuits (ICs) and power ICs and is renowned for its high-performance solutions tailored to automotive, industrial, consumer, energy, and other applications. The company’s commitment to innovation ensures that its products deliver exceptional safety, efficiency and performance across various industries.
Allegro's ACS series offers high-performance Hall-effect-based current sensor ICs designed for precise and reliable current measurement in various applications. Source: Allegro MicroSystems
For current sensing solutions, Allegro's ACS series stands out, as it offers a range of Hall-effect-based current sensor ICs designed for measuring AC and DC currents. These sensors are developed to meet the needs of modern industrial, commercial and communications systems.
Feature |
ACS37041 |
||
Package Type |
4x4mm QFN |
SOT23-W |
3mm x 3mm QFN12 and SOIC8 |
Current Sensing Capability |
Up to ±200A |
Up to ±30A |
Up to 60 A (QFIN12) and 55 A (SOIC8) |
Isolation |
Below 100 V(RMS) |
Below 100 V(RMS) |
420 V(Peak) 297 V(RMS) |
Ratiometricity |
No |
No |
No |
Overcurrent Fault Detection |
Yes |
No |
Yes |
Other Features |
ultra-low resistance (100 μΩ), AEC-Q100 certification |
Low resistance (1 mΩ), error <±5% over temperature range |
Immune to stray magnetic fields, fast overcurrent fault output, AEC-Q100 qualified |
Applications |
Optimized for automotive, industrial motor drive and data center applications |
Smaller package for size-constrained applications |
Highly versatile solution for current measurement in applications like solar inverters, consumer electronics, white goods, and various other places where power supply monitoring is required. |
Conclusion
Heat generation, large PCB footprints and design complexity are significant challenges for traditional methods of current measurement. Switching to Allegro’s magnetic current sensors offers numerous benefits, including precise and reliable current measurements, enhanced safety through electrical isolation and superior performance in both AC and DC applications. These sensors are highly accurate, temperature-stable and capable of reducing power losses compared to traditional methods. They are ideal for improving efficiency in motor control, power management and various other applications.
Visit Allegro Microsystems' official website today to find the perfect solution for your current measurement needs.